5 tips for conducting a successful virtual Factory Acceptance Test (FAT)
- Joseph Winslow
- Oct 19, 2020
- 4 min read
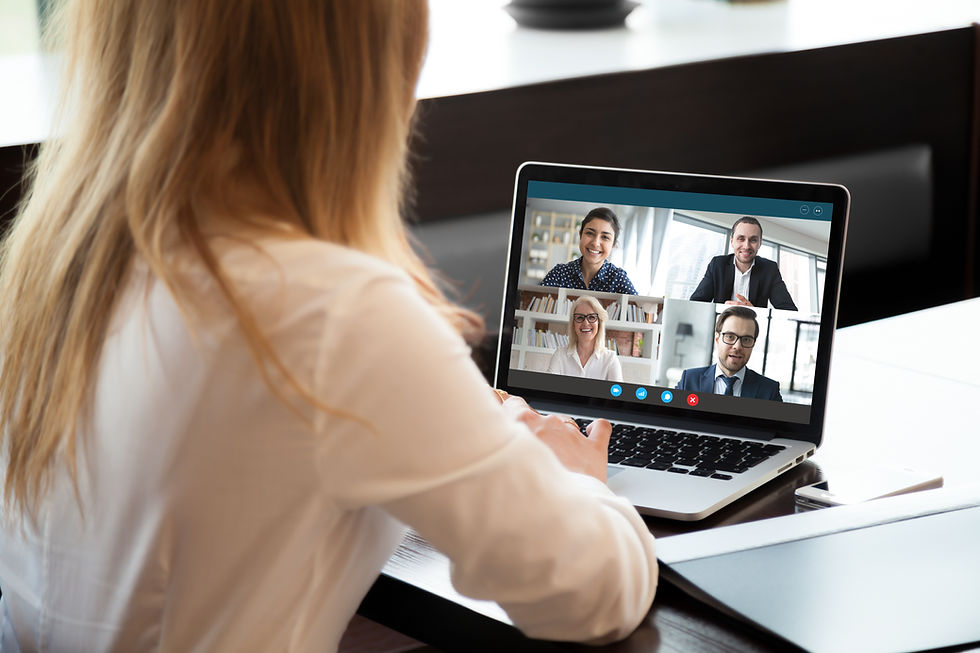
In the current climate of stay at home orders, social distancing and travel restrictions, there is still a need to get business done. “getting business done” means a lot of things, but in the BioPharma Industry, one of those things is the need to ensure that when equipment arrives on site, it works as intended and that the company gets exactly what it paid for. That need has been traditionally filled by conducting a Factory Acceptance Test (FAT) for equipment, especially for equipment that is customized for the client.
The FAT consists of writing and executing a protocol to test the equipment build and functionality at the factory prior to shipment. There are a couple of good reasons for performing a FAT. First, anything that is found wrong, can be fixed much more efficiently while the equipment is still at the factory by the same people who built it in the first place. Second, payment terms can be tied to a successful FAT which ensures that the client maintains some leverage over the equipment vendor by withholding payment until they are satisfied that they are getting what they paid for.
So, if “in-person” FAT’s are more difficult or impossible to conduct these days, an alternative is to conduct a virtual FAT over video conferencing. There are some obvious differences though, so here are some things to keep in mind to help make your virtual FAT successful.
1. Planning is key. It may seem obvious, but one thing you want to ensure is that your technology of choice works, and the equipment vendor is comfortable with it. You do not want to spend precious time solving technology issues when you are supposed to be testing your new equipment. It may be preferable to use the equipment vendor’s video conferencing software of choice so that they are most comfortable with it. Make sure that the technology at the factory end is on a mobile device so the client is not trying to watch the feed from across the room. There will be items that you want to see up close. Make sure the quality of the camera is top notch so that it focuses quickly and up close and provides a clear video feed.
2. Another planning item is the protocol itself. You should always strive to make the protocol clear and understandable, but when the writer is not physically at the FAT during execution, it can be even more important. Regardless of whether the client or the equipment vendor writes the protocol, it is a good idea to send the protocol to the other party ahead of the actual FAT so that they can read it and let you know if they have any concerns around being able to meet all of the requirements. It also provides an opportunity to see the sequence of tests to help with their planning process. Filling out the protocol should take place at the client end of the call, but if the equipment vendor knows the expectations and what the documentation requirements are, they can manage their own expectations on how long the execution will take.
3. Consider recording the FAT at both ends of the call so you have one recording as a back-up, and so you can be sure to be able to hear both ends of the conversation. Most video conferencing software has this feature built in, so make sure you know how to use it ahead of time. It is also a good idea to add steps into the protocol to start and stop the recording, so you do not forget those steps. Documenting in the protocol that it was conducted virtually is also a good idea. You can even add a link in the executed protocol to the video recording so they can be linked for future reference.
4. If possible, get the equipment operations and maintenance manual as well as all equipment drawings sent to you either electronically or on paper before the day of the FAT. When you are at the factory, it is easy to look at it for questions that may come up, but if you have ever tried to look at a document over an internet connection, you know it is less than ideal. And you will be referencing those documents during the FAT.
5. My final suggestion for a successful virtual FAT may sound silly at first, but it can help on the day of execution. Get one representative from the client and one from the equipment vendor to do a dry run ahead of time without the entire team in attendance. Oftentimes, because the virtual FAT does not require travel and extra expense, more people from the client will want to participate. If you can work out any bugs ahead of time during a dry run, it will keep the actual execution time to a minimum. It can also help the person responsible at the client look more professional and like they have things under control in front of the whole team.
Pro-tip: some tests like point to point checks can be tedious and time consuming, so you may want to consider executing those before getting the entire team involved.
There is nothing that can guarantee that your virtual FAT will go off smoothly, but the suggestions here can certainly help to make that a higher probability. Virtual FAT’s are here in the time of COVID and they are probably here to stay if we can learn to do them smoothly and convince everyone involved that the FAT was executed thoroughly. Virtual FAT’s can save time and money for both the client and the vendor so we should do what we can to make them successful.
Comentários